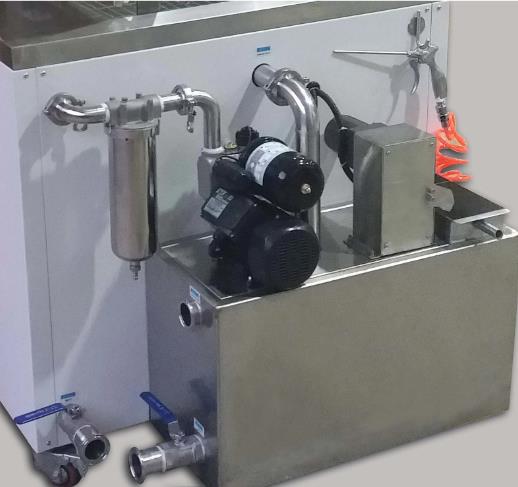
When using an ultrasonic cleaning system the object that is to be cleaned is put in an appropriate container that contains a solution (either in an organic or water-based solvent in accordance with the use). When using water-based cleansers surfactants (such like laundry soaps) are typically added to dissolve non-polar components like fats and oils. Transducers that generate ultrasonic waves are either built inside the vessel or dropped into the liquid to generate ultrasonic waves inside the liquid, by altering its size of the signal, which oscillates at an ultrasonic frequency. These create compression waves within the liquid in the tank that "tear" the liquid, leaving millions of tiny "voids"/" partial vacuum bubbles "(cavitation). The bubbles break up with tremendous energy, and can be triggered by temperature and pressure of up to 5,000 degrees Celsius and 135 MPa. They are however so tiny that they are able to only eliminate surface dirt and other contaminants. The greater the frequency, the smaller the number of nodes between cavitation points, which permits cleaning more intricate and complex parts.
Most hard, non-absorbent materials (metals, plastics, etc.) that aren't chemically attacked by cleaning fluids can be used for ultrasonic cleaning. Materials that are ideal for ultrasonic cleaning are small electronic parts, cables rods, wires, and small items such as details, as being made of aluminum, plastic, glass or ceramic.
Ultrasonic cleaning doesn't cleanse the object that is cleaning, as the spores and viruses may remain following cleansing. In medical settings sterilization is typically carried out as a separate procedure following the ultrasonic cleaning.
Industrial ultrasonic cleaners are utilized in the sports, automotive printing, marine pharmaceutical, medical disc drive, electroplating parts manufacturing and weapon industries.
Ultrasonic cleaning can be utilized to clean pollutants from industrial equipment, such as the heat exchangers and pipes.
More than 10 years they have demonstrated their reliability in their service, working flawlessly day in and day out with very little downtime. They have lower noise levels than the majority of other compressors and vacuum pumps.
The Side Channel Blower comes with several options available that can perform from 3,000 to 3,000 m3/h differential pressures as high as 1,000 millibars. They can be adapted and robust enough to meet the diverse requirements.
Dereike Series Side Channel Blowers utilize motors with voltage ranges between 50-60 Hz. They also have as well as protection Class IP55 (Insulation Class F) and UL 507 as well as CSA 22.2 The Dereike Series Side Channel Blowers have no. Certification 113. This makes them a perfect solution for worldwide use and use throughout Europe, Asia, and the Americas without modifications and conducting tests. They are generally sold off the shelves and are ATEX certified.
Advantages in an enumeration:
Stable and durable virtually maintenance-free
Up to 20.000 hours of operation, with zero downtime for maintenance
Some downtime could be as long as 40,000 hours of downtime without maintenance
Light and strong
Worldwide Use (UL/CSA/IEC/EN certification)
50/60 Hz motor
ATEX 94/9 EG
The speed can be controlled via an external or integrated frequency converter of all models.