Today, dry-screw vacuum pumps are used in chemical processing technologies and many other applications, just as dry-claw vacuum pumps have become the standard vacuum generator for entire industrial sectors. Oil-lubricated rotary vane vacuum pumps are also state-of-the-art in many applications, especially due to their continued development. They are generally the most used vacuum pumps in their field of application. Despite many improvements, new developments and further advances, one principle of vacuum generation has remained and is still used successfully in some applications: the liquid ring vacuum pump.
The principle behind the liquid ring vacuum pump was developed as early as 1890 as the "water ring pump". Due to their simple yet robust construction, liquid ring vacuum pumps (FIG. 1) are ideal for vacuuming wet gas or steam or for applications where condensation is likely to occur inside the vacuum pump during compression. They are therefore well suited for wet processes and can therefore be used in process technology, chemical industry, petroleum production and processing to generate coarse vacuum, ventilation of steam turbine capacitors, plastics industry, paper making, food technology industry and many other industrial applications.
The working principle of
As a working fluid, liquid ring vacuum pumps use water or a liquid compatible with the gas or steam to be vacuumed. Ethylene glycol, mineral oils or organic solvents, and other liquids that are already part of the process are also used. The basic principle is the same in all sizes and versions.
An eccentrically mounted impeller rotates within a cylindrical housing (FIG. 2). The housing is filled with working fluid so that the blades of the impeller are immersed in the fluid. The rotating motion of the impeller and the centrifugal force generated make the liquid in the shell form the so-called liquid ring. The gas is pumped into the Spaces between the blades and the liquid rings. Due to the eccentric arrangement of the impeller, the volume of these Spaces changes, resulting in gas being sucked in, compressed, and expelled again. The liquid ring seals each space to the cylinder. This is why it is sometimes referred to as a sealing fluid rather than a working fluid.
mechanism
Due to the working fluid used, the mechanism can only be used in the coarse vacuum range. The reason for this is that the degree of vacuum attainable depends on the vapor pressure and the viscosity of the working fluid, which is continuously pumped through the vacuum pump. This allows liquid ring vacuum pumps to operate at relatively low temperatures. It also operates mainly under isothermal conditions. This means that the medium to be pumped hardly heats up during compression. This is why liquid ring vacuum pumps are almost destined to suck vapors and gases with a high moisture content. The low temperature in the vacuum pump facilitates the condensation of wet steam and gas. In a way, this meant that the vacuum pump also acted as a capacitor. Because when the gas into the vacuum pump has been condensed, so the volume of the gas is greatly reduced. In addition to the condensation effect, this also achieves an increase in nominal pumping speed.
The working fluid transfers compression heat, a process that supports condensation and increases pumping speed.
A significant advantage of liquid ring vacuum pumps is that the working fluid and materials used in the components can be adapted to the pumping medium. This also makes it possible to pump explosive gases and vapors. Because of the low operating temperature, pumping explosive materials in any case has far fewer problems than other mechanical vacuum pumps.
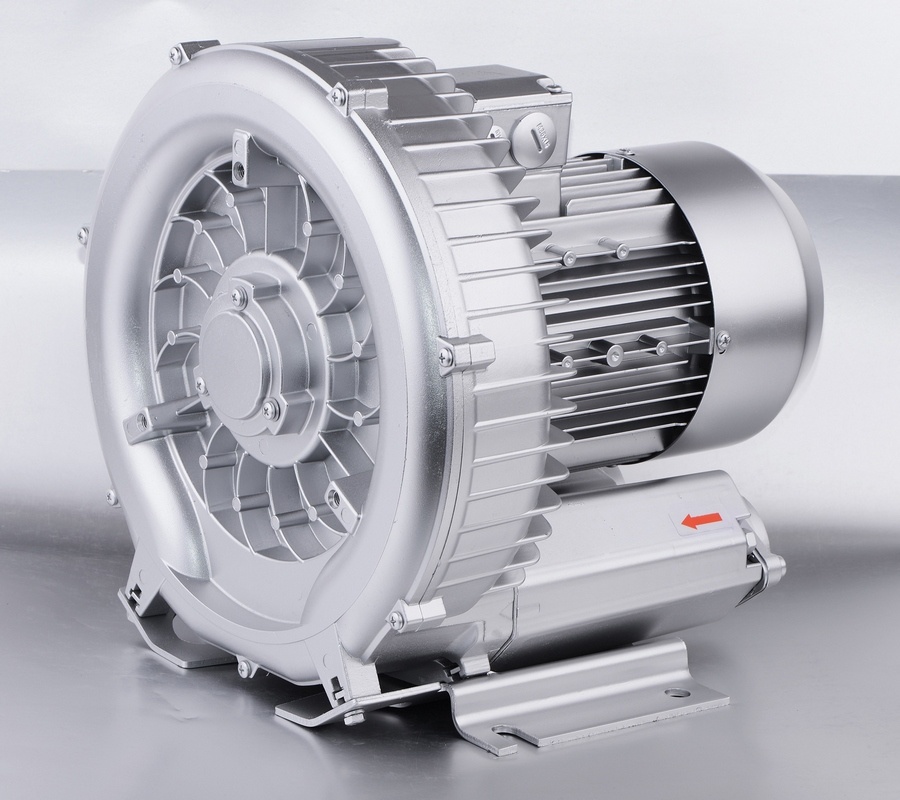
To build
Primary and secondary liquid ring vacuum pump basic difference. In the first level version, the above compression process is performed in a compression level. In a two-stage vacuum pump (FIG. 3), the pre-compressed pumping medium from the first stage is transported to the second compression stage and compressed again. The first-stage liquid ring vacuum pump version achieves ultimate pressures of 130 hPa (mbar), while the two-stage version achieves ultimate pressures of up to 33 hPa (mbar).
Even size varies greatly. Dereike Vacuum Solutions has different series and versions of the Dolphin liquid-ring Vacuum pump in its portfolio, with pumping rates ranging from 25 to 26,500 cubic metres per hour.