Side channel blowers are a popular and effective way to produce large volumes of clean, dry compressed air. They can also be used to generate a partial vacuum.
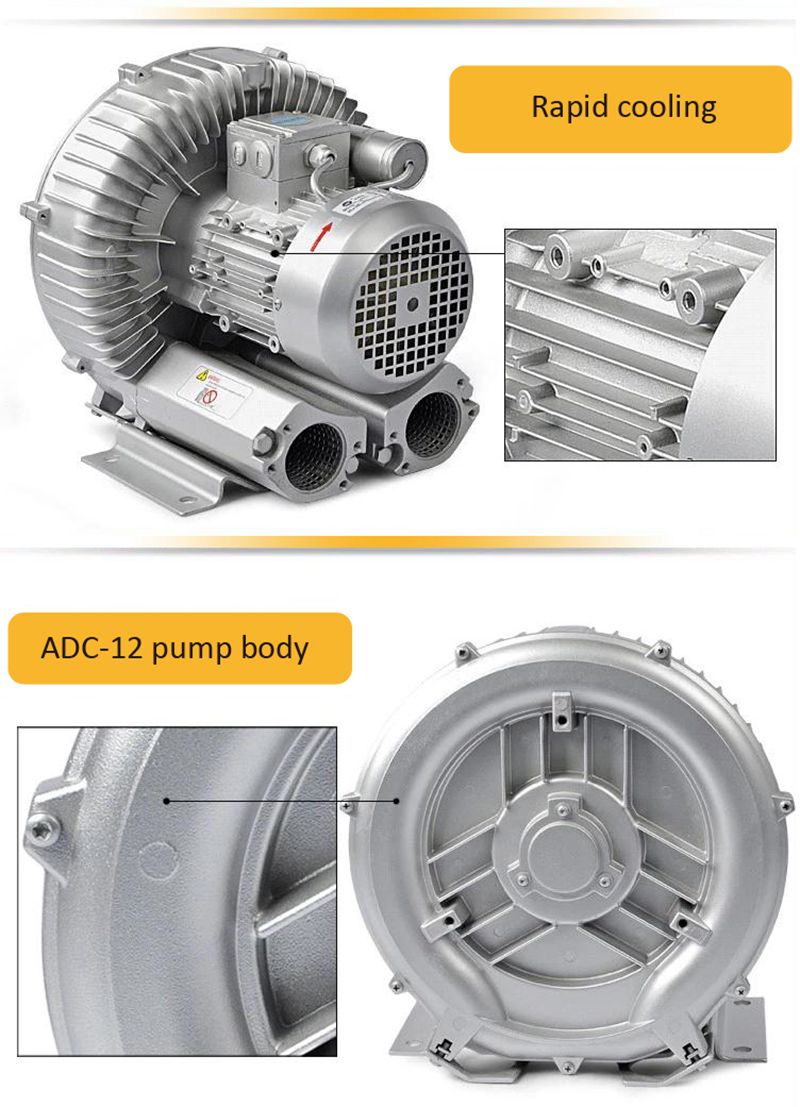
Side channel blowers can be defined as positive displacement, rotary machines used to move air or other gases. Their simple design makes them low cost and their non-contact configuration means they have no wearing parts so they are ultra-reliable. The design is such that the bearings are outside the compression chamber so are shielded from the heat generated during compression. As a result, maintenance is usually confined to regreasing the bearings every 28,000 hours of running time (typical usage over 10–20 years).
Side channel blowers are available in a wide range of sizes. The differential pressure they produce can be up to 1 bar. Blowers are manufactured using high pressure die casting methods, ensuring they are light in weight. Custom solutions are available to suit various user requirements. For instance, they can be supplied as bare shaft, with special motor voltages, internal coatings and surface treatments.
It is increasingly common for blowers to be used with variable speed drives (VSD), which allows them to be run in an energy efficient way and/or to be set to specific duty points. The VSD can be fitted externally to the blower, however EuroVacuum Products has just launched a new range of blowers with integral drives. These vary in size from 0.37kW to 5.5kW and are installed onto the electric motor, which allows the output of the blower to be adjusted to match the exact needs of the application.
Drives can be used as energy saving devices allowing the rotational speed of the blower to be reduced to the lowest allowable frequency to a ‘tick over’ value when output is not required. Blowers are also suitable for environments designated as potentially explosive atmospheres.
Another characteristic of side channel blowers is that they are quiet in operation, achieved through the addition of a silencer at the outlet, making them suitable for applications where noise would be an issue. Their operating principle is based on an impeller blade design that stirs the air into a spiral flow or vortex. This creates a dynamic pressure differential with low pressure at the centre or axis of rotation and increasing pressure towards the edge of the vortex. This pressure gradient forces the air or gas to follow a curved path until it reaches the outlet of the blower where it is expelled as compressed air or gas.
As a result, blowers produce suction or vacuum at the inlet and positive pressure at the outlet. Connecting to the inlet or outlet allows the user to generate suction or compressed air, as required. Side channel blowers are designed so that the impeller is driven directly by the motor; there are no engaging parts or mechanisms that could wear, break or require maintenance. The pressure generated by side channel blowers is relatively low compared to rotary vane and reciprocating compressors, but it is sufficient for many applications. For greater compression, two and three-stage design side channel blowers can be used.
Because they are robust, reliable and economic, side channel blowers have been used in many application areas. For instance, they are used in fume extraction, as well as cooling and drying in many different industries. They are also commonly used to drive air knives, which produce a high intensity, uniform laminar airflow for blowing liquid and/or debris from products. In waste recycling they can separate lighter materials from heavy ones by blowing them into a different process line.
In water treatment plants, they are often deployed to aerate water by blowing air into it via a membrane diffuser, which serves to regulate the size of the bubbles, (the smaller the bubbles, the greater the amount of water that comes into contact with the air). Similar techniques can be used in chemical engineering processes and, on a smaller scale, in laboratory applications. These versatile blowers are regularly used for pneumatic conveying, vacuum holding of work pieces in CNC machines and vacuum lifting of items such as sacks of vegetables.
Pneumatic conveying is probably the most efficient way to transport light granular materials such as the plastic pellets used in injection moulding and polystyrene beads used for packing delicate products. The basic principle is to blow the material along pipes towards its destination, with side channel blowers providing the compressed air for the driving force.
A variation on this principle is to blow cylindrical containers along the pipe, with the cylinders containing a load, often a sales order form or bank notes. Another form of pneumatic conveying is air table conveyors. With these a blower supplies air to a series of nozzles set in a tabletop, with each nozzle inclined upwards from the horizontal along the axis of the table. This sets up a laminar flow of air along the table so that lightweight
products can be carried from one end to the other, hovering on a cushion of air. In what is virtually a reversal of the air table conveyor design, blowers can be used in vacuum mode to hold work pieces securely in place on CNC machines. A typical example of this is two-dimensional cutting of cloth, wood and plastic. The advantage of this technique is the removal of the need for clamps or other holding mechanisms, the opening and closing of which can add considerable time to a production cycle in repetitive operations.