Pneumatic Conveying
Introduction
Everything you ever wanted to know about pneumatic conveying.
You will learn:
What is pneumatic conveying?
The Three Types of Pneumatic Conveying Systems
How to Choose a Pneumatic Conveying System
Pneumatic Conveying Design
And much more…
This diagram shows the process of pneumatic conveying
image by: www.vac-u-max
Chapter One – What is Pneumatic Conveying?
Pneumatic conveying uses compressed air, or gas, to transfer bulk materials, like powders and granules, from one processing center to another. Material is moved through an enclosed conveying line or tube using a combination of pressure differential and airflow from a blower or fan. The positive or negative pressure, inside the conveying line, moves materials safely with little damage or loss.
Pneumatic conveying systems transport cement, fly ash, starch, sugar, salt, sand, plastic pellets, oats, polymers, lime, soda ash, plastic resin, plastic powder, dry milk, and feeds in a cost and energy efficient way from railcars, trucks, or silos. Other uses of pneumatic conveying include intermodal or transloading, in plant transfer, and dust control.
The process of pneumatic conveying is a combination of well-engineered components that work together to move substances and materials safely, efficiently, and economically.
Chapter Two – Types of Pneumatic Conveying
The forms of pneumatic conveying are dilute phase, dense phase, pulse dense phase, and semi-dense phase. Each type moves materials using air pressure and an enclosed line or tube. The difference between them is their method of creating air pressure and how the material travels through the system.
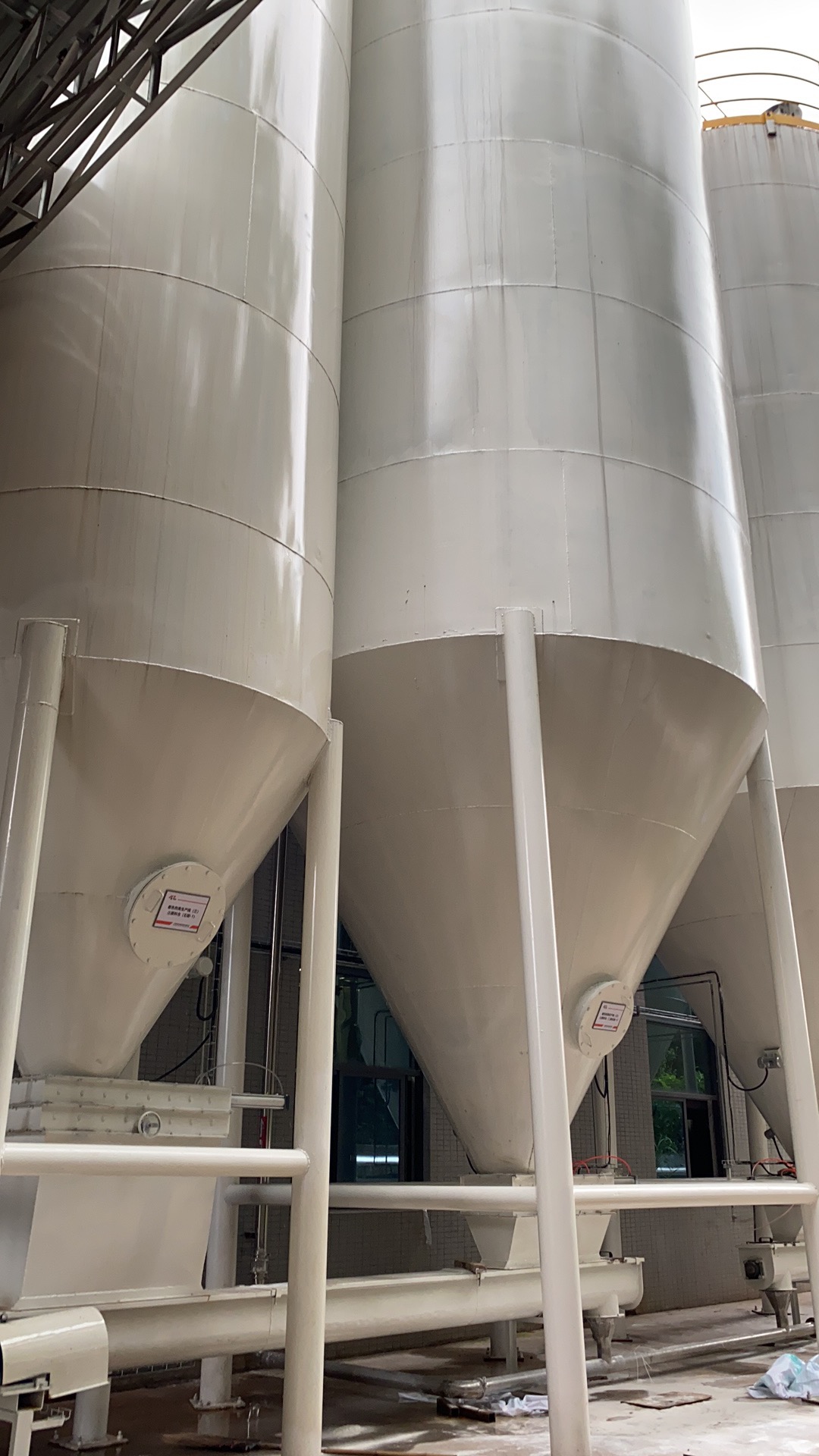
Types of Pneumatic Conveying
Below are brief descriptions of each method.
Dilute Phase
There are two methods for moving materials using dilute, suspension, or lean phase pneumatic conveying, which are positive and negative. A positive or blowing phase system uses a fan or blower to create pressure in the line and suspend the material. At the end of the line, the material is removed using a separator or filter. Materials travel between 15 meters per second to 35 meters per second (m/s).
Negative pressure systems, or vacuum systems, work in reverse. Instead of pushing or blowing material through the line, they create a vacuum and pull material through.
The difference in the two systems can be seen in the diagram below. In the vacuum system, on the left, the blower is located on the right with the hoppers on the left. In the pressure system, on the right, the blower is to the left of the feed tube pushing the material to the storage silo.
Vacuum Conveying vs. Pressure Conveying ()
Dense Phase
Dense phase pneumatic conveying uses a small amount of air to move a large amount of material in slugs, much like extruding. A dense phase system pushes a denser concentration of bulk solids at low velocities, as can be seen in the diagram below.
The Dense Phase pneumatic conveying uses “booster pulsers”, known as “air saver boosters“ or “air fluidizers”, to move the product and free it from the piping walls. Multiple controls or fluidizers are installed through the wall of the hopper section and the wall of specific pipe runs to loosen the material and direct the airflow, which inputs small shots of air to control the solidity of the product and maintain pipeline velocity.
Since the conveying pipeline is densely packed, air does not get past the material, which improves efficiency. Very few particles of the material make contact with the piping or tube, which reduces pipe abrasion and wear. The density decreases the transfer rate and pipe diameter, which increases velocity control.
Dense phase is perfect for fragile materials and mixtures because of its low speed and air volume, which prevents materials from breaking down.
Dense Phase Pneumatic Conveying (from )
Semi-Dense Phase
Semi-dense phase is an alternative between dense and dilute phase conveying. Materials travel at a medium rate velocity of 1500 to 3500 ft/min, which is higher than dense phase but lower than dilute phase. It is the perfect solution for transferring aeratable abrasive and friable materials. Semi-dense pneumatic conveyors provide increased speed with protection of the material.
Pulse Dense Phase
In pulse dense phase, material moves in a plug flow fashion. It is ideal for abrasive materials. A pulse pump separates the product into ‘plugs’ using an air knife. The plugs slide through the pipeline, as can be seen in the pipe diagram below. The benefits of a pulse dense phase system are a smaller pipeline, low air consumption, and less degradation of products.
Pulse Dense Phase System (from turbokopar)
Chapter Three – Choosing a Pneumatic Conveying System
Pneumatic conveying is a safe and efficient method for transporting materials and is used in thousands of industries. Entire books, journal articles, and white papers with diagrams and complicated equations have been written to understand its intricacies.
When exploring pneumatic systems, as a transportation method, there are factors that have to be considered. The equipment and method of conveying has to match the material to be transported. Below are a few guiding points to consider when choosing a pneumatic conveying system.
Characteristics of the Material
The first consideration when choosing a conveying system is the type of material to be handled. Bulk density is the first consideration since it determines vacuum receivers and sources of air. The bulk density determines how many cubic feet per minute is needed in the conveying line. Other factors to be considered are:
Particle size/shape
Friability
Moisture content
Abrasiveness
Toxicity
Explosive properties
Dry Bulk Materials (from )
Knowing the characteristics of the material is essential since each pneumatic system is designed to handle only certain types of materials.
System Size
It is important to understand if the system will be able to handle the distance, vertical or horizontal, the material will travel and if it will fit inside the facility. The size of the system has to leave room for maintenance and oversight. The system picture below is a complex vacuum system connected to container storage units.
Other factors include the number of pickup points, the size of the receiving container, if the process is continuous, feed rate, and if it is a batch process how often the batches will arrive and the size of the batches.
Vacuum Pneumatic Conveying System with a Container System (from )
Vacuum vs Pressure
A vacuum system sucks materials through the pipeline and is ideal for pressure sensitive non- abrasive materials. A pressure system pushes material through the pipeline and can move abrasive materials. Quartz and copper sulfate are the types of abrasive materials that a pressure system will move.
Non-abrasive powders conveyed by a vacuum pneumatic conveying system are moringa powder and powdered metals.
Moringa Powder (from nuts)
Powdered Metal (from inertcorp)
Dilute Phase vs Dense Phase
Dilute phase moves materials at high velocities under pressure and has some breakage during transport. Dense phase is used for fragile materials since it operates at low pressure. Dilute phase has a high air to product ratio, while dense phase has a low ratio. The image below shows the difference between dilute phase on the left and dense phase on the right.
Dilute and Dense Phase Pneumatic Conveying (from iedco)
Cost
The initial cost of a pneumatic conveying system can vary between several hundred thousand dollars for a complex system designed to move huge amounts of material to tens of thousands of dollars for a simple system. The first image below is a complex food conveying system designed to move tons of raw materials for food production. The second image is of a less complex straight material handling system for conveying powdered materials.
Unloading Conveying System for Powders for the Food Industry (from coperion)
Dry Material Handling (from pneumaticconveyingsolutions)
Chapter Four – Pneumatic Conveying Design
All pneumatic systems use pipes or ducts to transport materials on a stream of air. An air mover generates pressure or a vacuum and is located in the system at the beginning to push materials through the line or at the end to pull materials through.
The basic components of a pneumatic system are:
1.Pressure blower or vacuum pump
2.Rotary airlock valves
3.Conveying line
4.Diverter valves
5.Filter receiver
6.Cyclone separators
7.Batching systems
8.Hoppers
9.Controls
Components of a Pneumatic Conveying System
Pressure blower
Pressure blower is one of the two methods for moving material using a pneumatic conveying system. When designing a system, a major factor is the amount of pressure drop throughout the system, which is the most extensive at the end of the system. The force of the blower determines the flow rate at cubic feet per minute (CFM), velocity in meters or feet per second, and the pressure. It pushes the material down the pipeline.
Pressure Blower (from nyb)
Vacuum pump
Vacuum pump is another method of moving material. Vacuum systems are often used as part of a dilute phase system but can also be applied to dense phase systems. An electric driven vacuum pump is the most efficient and recommended method for producing the vacuum. As can be seen in the diagram, the vacuum conveyor is located to the right at the end of the pneumatic pipeline and pulls the material through.
Lean Phase Vacuum Conveying (from technolinksglobal)
Rotary airlock valves
Rotary airlock valves are used for handling solids when it is necessary to separate two areas under pressure, while moving the material from one condition to the next. They are used at the beginning and end of a pneumatic conveying system.
(from www.hmicronpowder)
Conveying line
Conveying line contains the material and method of transport, as can be seen in the diagram below.
(from unitedstatessystems)
Diverter valve
Diverter valve prevents contamination and provides line switching as can be seen in the diagram.
Diverter Valve (from vortexblobal)
Filter receivers
Filter receivers contain and separate dust from material in a pneumatic conveying system. The unwanted airborne material is trapped in the filter in the receiver unit as seen in the diagram on the right.
Filter Receivers (from powderprocess.net)
Cyclone separator
Cyclone separator uses centrifugal force to remove particles from air in a pneumatic conveying system. Air enters the cyclone whose rapid rotation separates the particles, which are blown against the wall and fall to the bottom of the container.
Cyclone Separator (from unitedstatessystems)
Batching system
Batching system uses pneumatic conveying for mixing ingredients that are injected into the conveying line and forwarded into a mixture. Batching operations dramatically increase the size of a pneumatic system.
Ingredient Batching System (from iqh-internet)
Hopper
Hopper contains the material before it is introduced into the conveying line. A rotary airlock valve releases the material from the hopper as can be seen in this diagram of a chip hopper feeding a conveying line.
Dense Phase Pneumatic Metal Chip Conveying System (from nationalconveyors)
Controller
Controller is a necessary part of a pneumatic conveying system and is designed to fit the needs and configuration of the system. Common controllers are microprocessors or PLC based. They are designed to control blower and filter operations, valves, receiving hopper control, loaders, and filter pulsing using a PC.
VIEW MANUFACTURERS >>>
Chapter Five – Pneumatic Conveying Control Systems
Pneumatic conveying systems require immediate responses to changes in the conveying line. When a storage container is full and the system has to switch to another container, the system has to react and adjust the volume and airflow. Maintaining these changes, and adjusting to them, is the reason for pneumatic control systems.
The Benefits of a Pneumatic Conveying Control System
Selection of conveying modes
Cost savings
Quicker startup
Intuitive operation
Connectivity
Remote diagnostics
Control air consumption
Batching and weighing
Process Controls and Automation
An airflow controller continually assesses the demands of the system and provides instant feedback. The system measures material mass flow rates and makes adjustments to keep it within the optimum range. Data collected from the system is used to analyze overall efficiency.
Closed loop controllers combine flow rate and process controls. The system stores data and calculates where leakage and errors will occur. Using the accumulated data the system makes adjustments and compensates for any problems. Using the pressure difference, density, and the temperature of the medium, the system calculates the best flow rate. The volume flow is adjusted by changing the stroke of the control valve creating less
Conclusion
Pneumatic conveying systems use compressed air, or gas, to transfer bulk materials, like powders and granules, from one processing center to another.
The positive or negative pressure in a pneumatic conveying line moves materials safely with little damage or loss.
Pneumatic conveying systems use pipes or ducts to transport materials on a stream of air.
Materials transported by pneumatic conveying systems include cement, fly ash, starch, sugar, salt, sand, plastic pellets, oats, polymers, lime, soda ash, plastic resin, plastic powder, dry milk, and feeds.
Pneumatic conveying systems are widely used because of their efficiency, cost effectiveness, and flexibility.